Plastics
Plastic Product Design Validation using SOLIDWORKS Simulation – Sales and Technical Support from EGS India since 1997
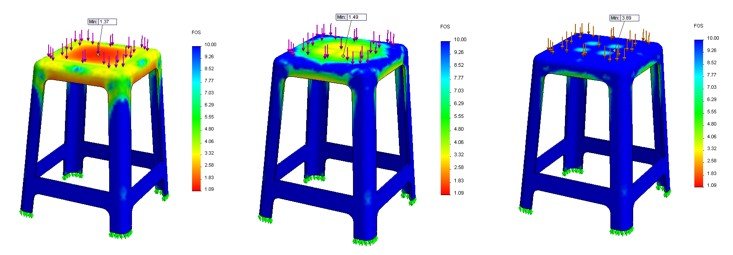
Household appliances, medical devices, electrical fittings among others incorporate numerous plastic product designs that need critical design validation to meet functional requirements. SOLIDWORKS Simulation finds extensive use in validating plastic product designs for functional efficiency and optimal usage of materials. Capabilities of SOLIDWORKS Simulation include:
- Snap-fit simulation for stresses and deflections
- Limit load analysis of critical load bearing components
- Strength calculations of reinforced plastics
- Kinematic analysis of actuation systems and mechanisms
- Optimization of designs for least cost and weight
Benefits of SOLIDWORKS Simulation for Plastic Product Design
SOLIDWORKS Simulation has been proven for design validation of many equipments used in plastic product design. Some of them include:
- Industrial and House-hold plastics ( such as Electrical )
- Automotive Plastics
- Food and Beverage Plastics
- Appliances, Toys and mass-produced plastic components.
SOLIDWORKS Simulation can be used to determine:
- Stresses and Deflections in load bearing members
- Natural Frequency and Velocities/ Accelerations due to operational requirements
- Least Cost and Weight Designs
- Stiffness and deflections due assembly torque
- Kinematic analysis of mechanisms using SOLIDWORKS Motion
- Selective Optimization to reduce cost and weight
- Fatigue Life prediction and Failure Mode estimation of load-bearing members and components
- Limit Load Analysis
Comments are closed.