Automotive
EGSIndia – Proven Partner for Applications of SOLIDWORKS Simulation in Automotive Design Validation – Sales and Technical Support in India
Being an affordable FEA solution, SOLIDWORKS Simulation has been well-received by the automotive industry for system-level as well as component level analyses involving critical design functions on one side and aggressive cost/ weight targets on the other. To be globally competitive, the automotive suppliers have used SOLIDWORKS Simulation to improve reliability, eliminate field-failures, optimize designs and enhance efficiency very easily. Specific capabilities include the following:
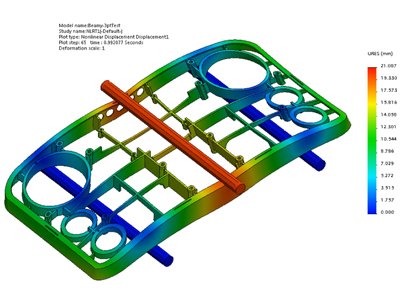
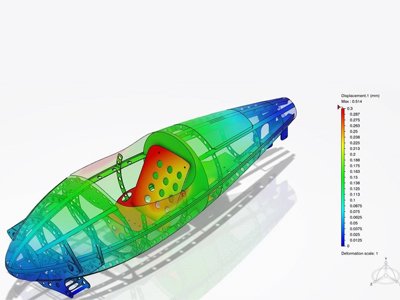
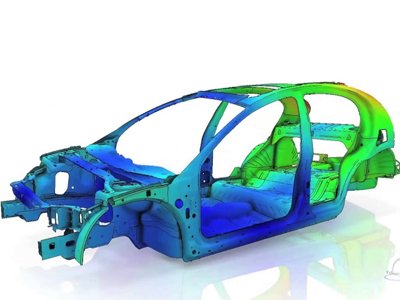
- Strength, Durability, Factor of Safety & Stiffness calculations for Body-in-White, Trim-body, Chassis aggregates
- Frequency response for multi-source excitations including Random Response
- Response to Fixed and Variable Frequency excitations with specified accelerations – Engine and Body mounted sub-systems
- Fatigue and Life Prediction Calculations
- Thermal management of braking and exhaust systems
- Evaluation of alternate materials to satisfy functional requirements
- Fluid Flow in Sub-systems such as Fans, Radiator, Centrifugal pumps and Turbo-chargers
- Thermal management of Engine Electronics
- Analysis-to-test correlations of strains, frequencies, mode-shapes, temperature, displacements, velocities and accelerations
- Full-vehicle simulation of vehicles, buses, trucks, utility vehicles, loaders, trailers among others
Advantages of SOLIDWORKS Simulation for Automotive Applications
- Wide range of Analysis – From components to Sub-systems to Full Systems
- Kinematic Analysis using SOLIDWORKS Motion for mechanisms such suspension, door and other closures, wiper systems, actuating linkages such as braking, acceleration and clutch sub-systems
- Non-linear Simulation of Elastomers, Tyres, Seals, Gaskets, re-inforced rubber components for strains, performance, durability, sealing effectiveness, pressure foot-print, deflections
- Stiffness, Durability, Tri-axial / Random Vibration and Life estimation for automotive components such as mounts, engine mounted systems and body-mounted systems
- Stiffness and strain calculations for sheet metal components, chassis sub-systems, transmission sub-systems, Body-in-white (BIW) and Trim Body
- Life Calculations of sub-systems such as wheels, suspension spindles, steering systems among others
- Fluid Flow calculations for pumps, pressure-regulating devices, radiator fans, engine-electronics cooling, braking system, power-steering fluid circuits, cooling circuits and lubricating galleries.
Return on Investment using SOLIDWORKS Simulation has been the highest among contemporary FEA Software. Design Optimization based on CAD models is easily accomplished in native CAD environment resulting in reduced time and cost.
Comparison with Contemporary FEA Software
Features | SOLIDWORKS Simulation | Other FEA |
---|---|---|
CAD Integrated FEA | ![]() | Limited or Expensive |
Design Scenarios | ![]() | ![]() |
Easy to Use | ![]() | Known as not easy to use |
CAD driven Optimization | ![]() | ![]() |
Analysis to test correlation using ‘soft’ ‘Sensors’ | ![]() | ![]() |
CAD Integrated Kinematic Analysi | ![]() | ![]() |
Automatic transfer of loads from Kinematic Analysis to FEA | ![]() | ![]() |
Special – SOLIDWORKS Simulation in Automotive Design Durability
SOLIDWORKS Simulation has been used in design and validation of automotive Tier I and Tier II suppliers. Some of the areas of application include:
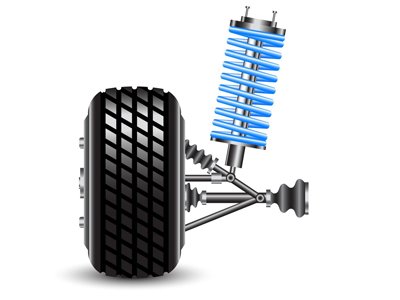
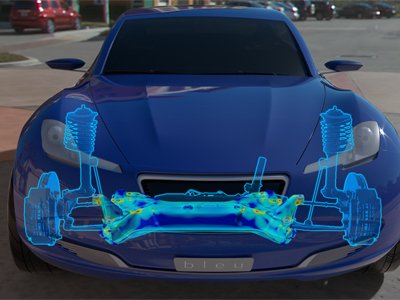
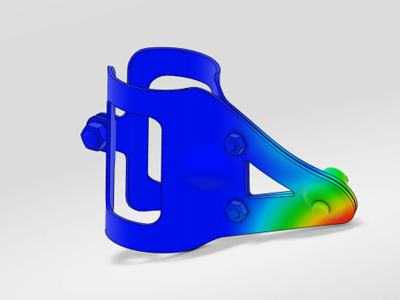
- Validation for Tri-axial Fixed Frequency and Variable Frequency Shaker Testing conditions
- Life Usage Factor calculation and Failure Mode Estimation
- Hot-chamber and Cold-chamber Testing of automotive sub-systems
- Fatigue and Life prediction of Suspension spindles, Lower control arms, high-cycle fatigue components
- Point Mobility Calculations for Engine mounts (achieving dynamic stiffness targets )
SOLIDWORKS Flow Simulation in Automotive Applications
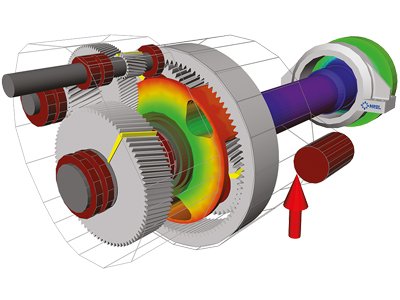
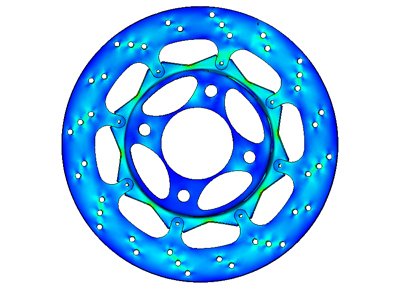
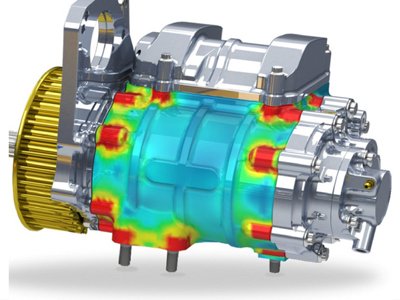
- Fluid Flow in Cooling – Engine, Braking, Under-hood electronics and electrical sub-systems
- Multiple Design Scenarios can be studied in CAD environment
- Embedded in SOLIDWORKS for Integrated Fluid Flow Simulation
- Thermal management of Braking Systems
- Flow in centrifugal pumps used in Engine coolant circulation
- Flow through carbuttors and fuel circuits
- Both Hierarchical and Polynomial Finite Elements for greater Accuracy and Speed.
- Cooling and Thermal management of engine electronics
- Parametric design studies of radiator configurations, fans and critical performance sub-systems
- Engineering Fluid Dynamics based on engineering parlance, goal-based optimization and proven CAE against test data
Comments are closed.